

In internal mixer two additional conditions have to be fulfilled. This is achieved by passing the polymer carbon black batch through a narrow nip either between two rolls of a mixing mill moving at frictional speed or that in between rotor tip and chamber wall of an internal mixer. To achieve dispersion of the carbon black, the polymer mass itself has to exert considerable shear stress on the carbon black agglomerate incorporated inside the polymer. CONDITIONS FOR GOOD DISPERSION OF CARBON BLACK Under tension, cracks develop at these spots.įailure properties like tensile strength, tear strength and consequently abrasion resistance come down as the degree of dispersion comes down. Undispersed carbon black (normally taken as carbon black agglomerates bigger in size than 9µm) act as gritty particles. Viscosity break down occurs during mixing and is essential for smooth processing of the stock.ĭegree of dispersion of carbon black has profound influence on the physical properties of the vulcanisate. Careful consideration is necessary not only as regards the time of the mixing cycle but also for the order of addition of ingredients to the rubber. Rebuild Farrel F270 Mixer From Pelmar Engineering Ltdĭispersion however is dependent on the shear stresses generated within the polymer and hence good dispersion may not be achieved by prolonged mixing.
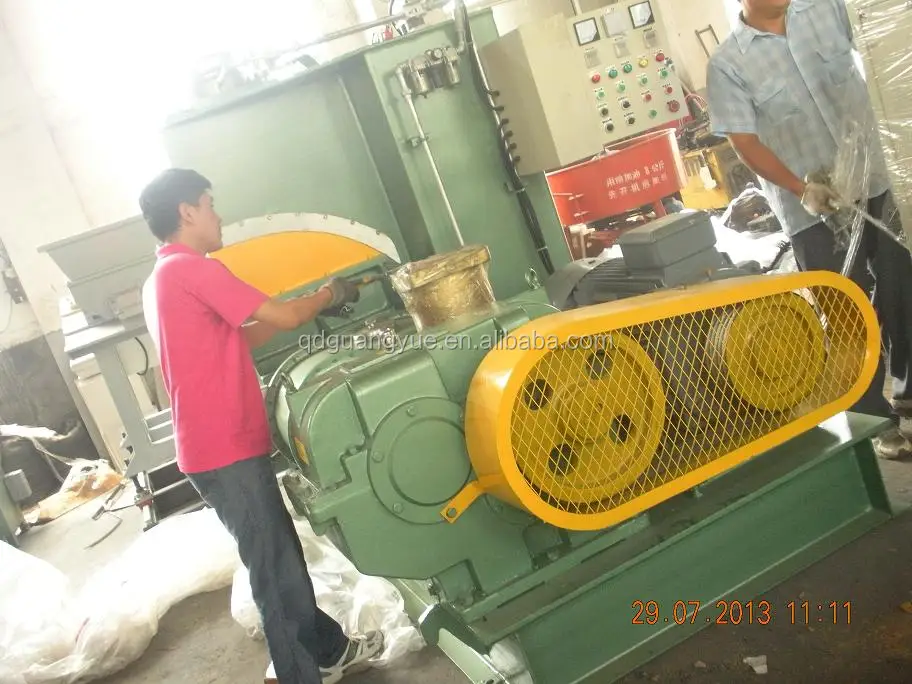
Good distribution is comparatively easy to achieve by paying proper attention to cutting and folding operations on a mixing mill or by just prolonging the mixing cycle in an internal mixer. Because of the large surface area of the powdered rubbers, the incorporation into polymer is very fast and only a very short mixing cycle in the internal mixer is adequate to achieve the mixing.Įven after all ingredient is incorporated, dispersion/distribution of the ingredient is not complete. The powdery mass is compacted in another machine and then fed to the internal mixer. In a simple ribbon blender the powdered rubbers can be mixed with the other compounding ingredients.
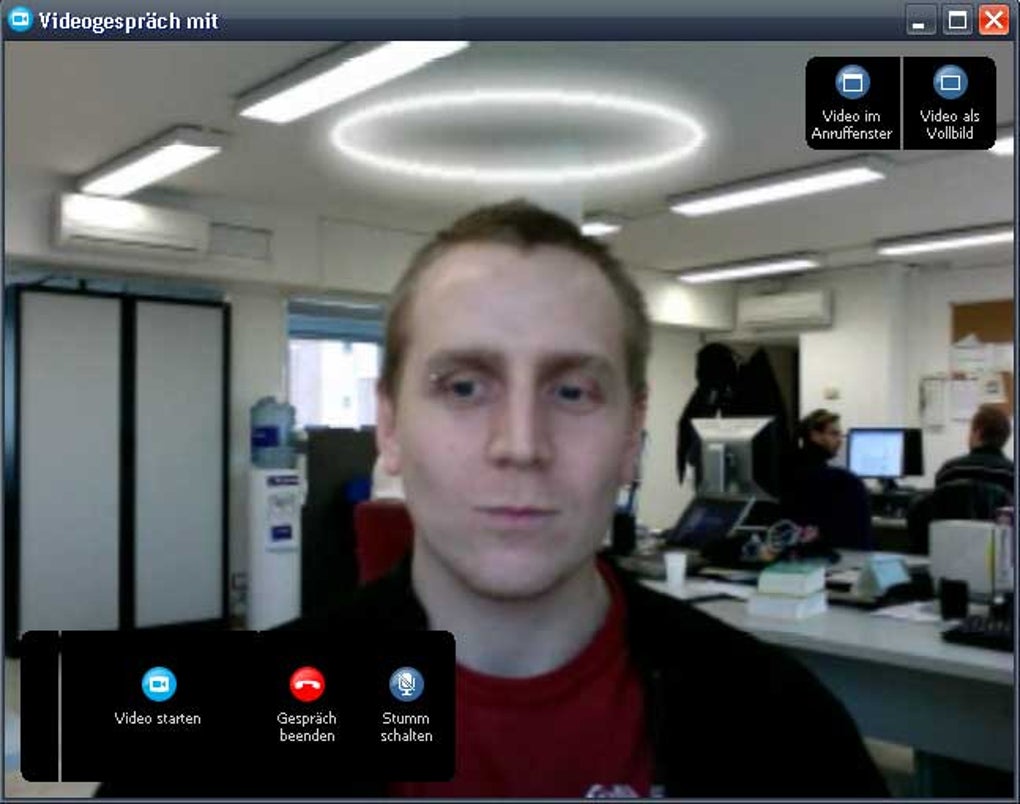
The ingredients incorporation is a very slow process.Īnother method of reducing incorporation time is to use powdered rubbers. This phase is also known as intensive mixing or homogenization in micromolecular level.ĭistribution or homogenization in micromolecular level or extensive mixing is “the moving of the agglomerates / particles from one point to another, without changing the shape of the particle to increase the randomness of the mixture”. Then these aggregates are absorbed or incorporated into the rubber to form a coherent mass.ĭuring mixing, shearing of the rubber generates shearing stress in rubber mass which imposes in turn shear stress on these aggregates and breaks these into their ultimate fine size which in case of carbon blacks is of the order of about 1µm. During subdivision large lumps or agglomerates are broken down into smaller aggregates suitable for incorporation into the rubber.įor instance carbon black pellets which have dimension of the order of 250-2000 µm get broken down into aggregates with dimensions of the order of 100 µm. The mixing of solid ingredients into the solid polymer occurs in phases.
